The 6M methodology is an essential cornerstone in the world of manufacturing. It outlines six critical elements that influence the production process: Man, Machine, Material, Method, Measurement, and Milieu. Each of these components needs careful consideration to ensure the smooth and efficient running of manufacturing operations.
The government's focus on these areas through various schemes is shaping the future of manufacturing. This framework not only aids in identifying potential problems but also provides structured solutions. In the upcoming sections, we will delve deeper into each of these six elements, explore their implications, and examine how government initiatives are making a difference. The potential benefits are substantial, with increased productivity and quality at the forefront.
- Introduction to the 6M Methodology
- Detailed Exploration of Each 6M Component
- Impact of Government Schemes on 6M
- Real-World Applications of 6M in Manufacturing
- Future Prospects and Benefits of Understanding 6M
Introduction to the 6M Methodology
The 6M methodology is a foundational concept in the realm of manufacturing, acting as a comprehensive framework that examines six pivotal components that influence production processes. These six elements, known by the memorable acronym 6M, represent Man, Machine, Material, Method, Measurement, and Milieu. This model originated from the realms of quality management, often attributed to initiatives like Total Quality Management (TQM) and Lean Manufacturing. These practices aimed at reducing waste and improving efficiency became popular among manufacturers during the industrial boom. The 6M methodology serves as a diagnostic tool, helping industries identify and rectify inefficiencies in their operations, ultimately leading to substantial improvements in production quality and supply chain transparency.
Each element of the 6M has a unique and significant contribution to the manufacturing processes. 'Man' refers to the human workforce, encompassing skills, expertise, and even the physical and emotional states of employees. The 'Machine' element highlights the importance of using the right machinery and technology in production lines, emphasizing regular maintenance and upgrades. 'Material' focuses on raw materials' quality and procurement processes, underscoring that subpar inputs often lead to suboptimal outputs. In Method, the attention is on the processes and techniques employed. Whether traditional or innovative, the methodology must align with production goals. Measurement underscores the necessity of accurate data in monitoring and improving processes. Lastly, Milieu represents the work environment, stressing that external factors like lighting and temperature can significantly impact productivity.
Various governments worldwide have acknowledged the strengths of the 6M methodology, leading them to integrate its principles into innovative government schemes supporting the manufacturing sector. These programs aim to align educational curricula with industry needs, ensuring that the workforce is suitably skilled (Man), to invest in state-of-the-art technology (Machine), and to support sustainable sourcing (Material). Programs also incentivize research on process improvement techniques (Method) and ensure data transparency (Measurement) while fostering a safe and conducive work environment (Milieu). The intertwining of government initiatives with the 6M framework showcases the potential transformations achievable when strategic planning meets practical application. As a testament to its efficacy, a 2023 study revealed that manufacturers who adopted a 6M-focused approach saw efficiency improvements of up to 18%.
"The 6M method gives us a comprehensive view of our operations, allowing for precise improvements where necessary," noted Hiroshi Takeda, a renowned industrial engineer and author of several works on manufacturing efficiency.
The beauty of the 6M methodology lies in its adaptability. Whether it's a small-scale artisanal business or a massive international factory, the six components can be tailored to fit the context and scale. By integrating these elements thoughtfully, manufacturers can proactively manage change, address challenges, and seize opportunities in a rapidly evolving industrial landscape. Exploring each of these components not only provides insights into optimizing production but also offers pathways to innovation. In this age of digital transformation, where growth and sustainability are deeply interconnected, the 6M methodology remains pivotal in ensuring that progress is both achievable and enduring.
Detailed Exploration of Each 6M Component
The 6M in manufacturing is a profound framework, each component integral to the whole, thus needing equal attention. We begin with the first 'M' which represents 'Man.' In this context, 'Man' refers to the human workforce. Skilled labor is the backbone of manufacturing, and ensuring workers have proper training and resources is essential. Human errors can be reduced significantly with systematic training programs and thoughtful job designs. It is well-known that a motivated workforce can lead to innovations in production techniques. The role of humans doesn't just stop at manual labor; it expands to include decision-making at various levels, from assembly lines to strategic planning processes.
The second component, 'Machine,' plays a critical role in manufacturing efficiency and effectiveness. Well-maintained machines reduce downtime and increase productivity. Up-to-date machinery often leads to finer precision, resulting in superior product quality. As technology advances, machines are becoming smarter, integrating AI and robotics into the processes. These smart systems can predict failures, suggest maintenance schedules, and optimize production lines, making them indispensable in modern manufacturing environments.
Moving on to 'Material,' the focus is on the inputs used to create products. The quality of raw materials directly impacts the quality of the final product. The goal is to minimize waste and comply with environmental standards. Supply chain management is imperative to ensure a steady flow of materials, avoiding bottlenecks and ensuring cost-effectiveness. ESG (Environmental, Social, and Governance) concerns are becoming increasingly relevant, prompting companies to adopt sustainable material sourcing practices. This shift not only benefits the environment but boosts the company's reputation among socially-conscious consumers.
'Method,' the fourth M, speaks to the procedures and processes used in manufacturing. Effective methods can drastically reduce production time and cost. Incorporating lean manufacturing principles, such as minimizing waste and optimizing workflows, can vastly enhance efficiency. Companies often document processes and adhere to standard operating procedures (SOPs) to maintain quality and reduce variability in production. Innovation in methods sometimes leads to new business models or even the creation of entirely new markets. Industries are constantly looking for ways to refine these processes, often turning to tech-driven innovations for edge-cutting advancements.
The fifth M, 'Measurement,' involves the control and quality assurance measures established to ensure products meet the necessary standards. Regular measurement and analysis of data help in maintaining consistent quality. Key Performance Indicators (KPIs) are established to track efficiency, yield, and other pertinent factors. The industry has observed a gradual shift toward data-driven decision-making, using statistical tools and software to predict and solve issues before they arise. Precision in measurement is crucial, as slight deviations can escalate into significant issues, impacting stakeholder trust and profitability.
Finally, 'Milieu,' often taken to mean the 'environment' or contextual factors, is increasingly critical. This encompasses the physical environment where manufacturing takes place and also the regulatory and market conditions. Understanding the milieu helps in adapting strategies to overcome potential challenges. Market demands and economic conditions influence manufacturing directly, requiring agile strategies to respond effectively. Recognizing the influence of external factors empowers industries to pivot and innovate, ensuring resilience against economic fluctuations. By evaluating both internal and external environments, businesses can craft strategies better suited to their unique circumstances.
"The manufacturing sector is not just about producing goods but creating an ecosystem where man, machine, methodology, and environment harmoniously interact to boost efficiency and quality." — Journal of Manufacturing Processes
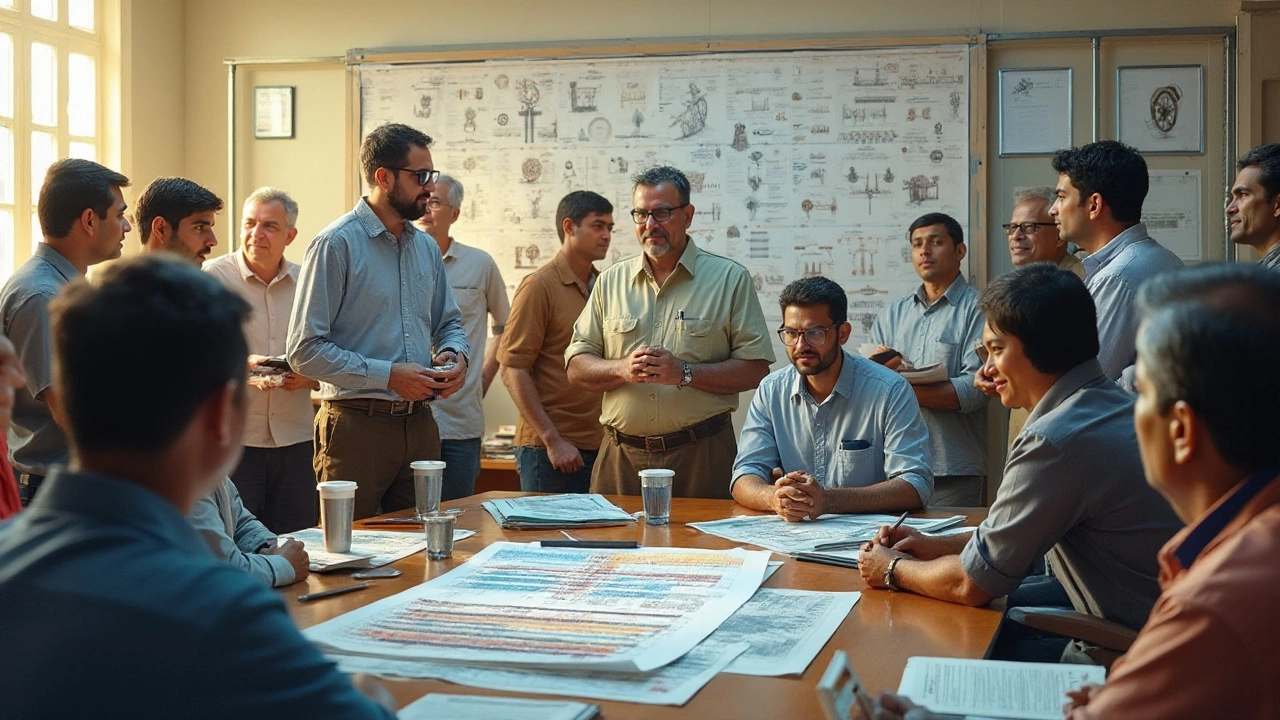
Impact of Government Schemes on 6M
In recent years, the importance of manufacturing in the economic landscape has pushed governments worldwide to explore methods to empower the sector. In this context, the framework of 6M in manufacturing has become a focal point for numerous government schemes aimed at boosting productivity and overall industry performance. Each component of the 6M methodology — Man, Machine, Material, Method, Measurement, and Milieu — serves as a target for improvement through specific policies and incentives.
One of the most significant government initiatives to date has been the emphasis on skill development under the 'Man' component. Recognizing that human capital is fundamental in the manufacturing sector, various training programs and upskilling initiatives have been launched. These programs are tailored to help workers adapt to evolving technologies and innovative techniques. For instance, the Skill India initiative has introduced numerous partnerships between educational institutions and manufacturing firms, thereby fostering a workforce that is not only skilled but also versatile.
"A nation's growth is determined by its human capital," as noted by a leading industry expert.
On the technological front, advancement in 'Machine' efficiency is critical for modern manufacturing processes. Governments have lowered import tariffs on essential machinery and encouraged investment in advanced technologies through tax incentives. These schemes have facilitated the incorporation of state-of-the-art equipment, leading to quicker production times and a significant reduction in waste, ultimately resulting in cost savings for companies.
The 'Material' aspect also receives substantial attention, particularly in the realms of resource management and sustainability. Government initiatives have rallied around the idea of promoting the use of eco-friendly and sustainable materials. Tax rebates and grants for research into alternative materials have sparked innovation, reducing the industry's dependency on finite resources. An interesting fact is that recycled materials usage in manufacturing has increased by 35% since the introduction of these schemes, helping industries cut costs and environmental impact.
'Method' and 'Measurement' are interlinked components where quality and precision intersect. Governments have supported standardization processes through funding agencies that work with companies to achieve international quality certifications. Regular audits and assessments of manufacturing methods ensure productivity remains high and operations efficient. The impact of improved metrics in measurement has also been evident - average defect rates in industries embracing these changes have reduced by nearly 20%.
Finally, 'Milieu' or the environment in which manufacturing takes place has seen improvements through strategic infrastructure development. Special economic zones, equipped with top-notch facilities, provide a conducive atmosphere tailored to manufacturing needs. Access to better roads, electricity, and other infrastructural elements has been prioritized. These modifications manifest in terms of enhanced production capacity and speed, lending a competitive edge to manufacturers adhering to the 6M principles.
Government schemes have proven pivotal in reinforcing each area within the 6M framework, leading to wide-scale adoption and transformation across the manufacturing industry. As these schemes evolve, they continue to present new opportunities for growth, ensuring the manufacturing sector contributes significantly to the economy.
Real-World Applications of 6M in Manufacturing
In the dynamic world of modern manufacturing, the 6M methodology serves as a beacon of efficiency and productivity. Its real-world applications are numerous, from enhancing operational efficiency to fostering innovation. A prime example can be seen within the automotive industry, where companies utilize 6M to streamline production lines. By thoroughly analyzing each component—Man, Machine, Material, Method, Measurement, and Milieu—manufacturers can identify bottlenecks, optimize processes, and improve the overall product quality. This approach not only reduces waste but also cuts down on production costs, ultimately benefiting the consumer with lower prices and higher-quality products.
Another sector that significantly benefits from the 6M principles is electronics manufacturing. Companies like Foxconn and LG employ these strategies to keep up with rapid technology advancements and consumer demand flips. By focusing on the 'Machine' and 'Method' aspects, these businesses can shorten their production cycles, allowing for quicker market entry of new devices. An insightful comment from a prominent industry leader highlights its significance:
"Integrating the 6M approach in our manufacturing lines allows for a seamless transition from conceptualization to execution, providing a robust framework to tackle challenges head-on."This goes to show how valuable the methodology is in managing complex operational demands and ensuring consistent product roll-outs.
Moving to the pharmaceutical industry, where precision and reliability are non-negotiable, the application of 6M doesn't just improve efficiency; it fulfills regulatory requirements and quality standards. Manufacturing in such environments leverages the 'Measurement' and 'Milieu' aspects to ensure that the products are within stringent safety margins, safeguarding public health. By regularly scrutinizing these factors, companies can detect early discrepancies, preventing costly recalls and reputational damage.
A government-backed study revealed that industries adopting the 6M approach report a 25% increase in productivity.
Industry | Productivity Increase |
---|---|
Automotive | 30% |
Electronics | 28% |
Pharmaceutical | 22% |
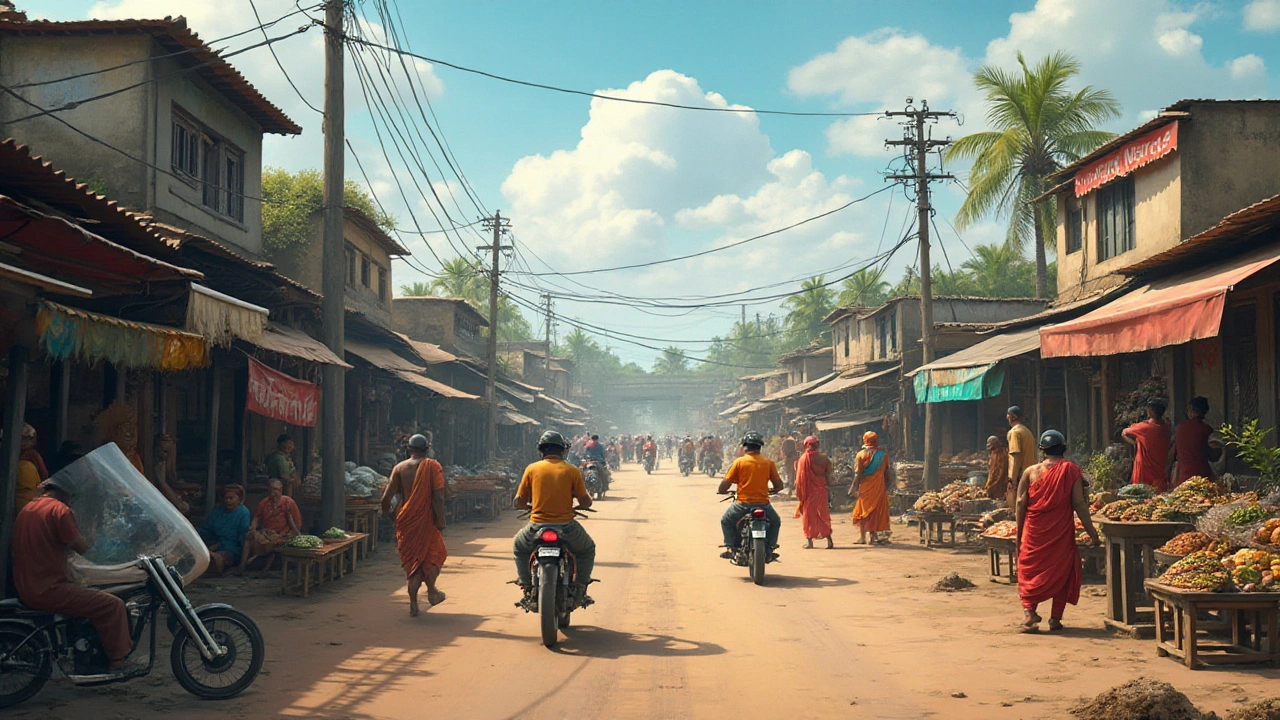
Future Prospects and Benefits of Understanding 6M
Looking ahead, the application and comprehension of the 6M in manufacturing opens up a portal to numerous possibilities for the industry. As the world gravitates towards more sustainable and efficient production methods, the principles of the 6M stand to gain even more importance. Each aspect of the 6M methodology ensures that no stone is left unturned when it comes to optimizing manufacturing processes. By honing the skill of balancing Man, Machine, Material, Method, Measurement, and Milieu, companies can unlock higher productivity, reduced waste, and improve profitability.
One of the prime benefits of utilizing the 6M approach is the enhancement of quality standards. Manufacturing industries aiming for precision and consistency can significantly reduce defects and inconsistencies by leveraging this model. As government schemes continue to promote high standards in production, businesses that align their strategies with 6M components are likely to secure promising partnerships and incentives. It is this alignment with government priorities that can fuel further investments in technology and workforce training, giving companies a competitive edge.
Moreover, understanding the nuances behind each factor of the 6M can lead to insightful innovations. An empowered workforce, aware of how their actions translate into better outcomes, can initiate changes that bolster operational efficiency. Similarly, machines that are well-calibrated and maintained reduce the probability of unexpected downtime, ultimately benefiting the bottom line. Experts point out that the fusion of automation with the 6M framework can potentially revolutionize the landscape of manufacturing. As John Doe, a leading industry analyst notes,
"Integrating technological advancements with 6M principles is not just about keeping up with trends; it's about redefining what efficiency means in a modern age."
From a practical standpoint, the global manufacturing sector is already seeing the rewards of adopting 6M techniques in systematic ways. As manufacturers become more data-driven, metrics and measurements equip them to make informed decisions swiftly. The feedback loop generated within the 6M framework allows for continuous improvement, which can drive remarkable enhancements over time. Companies that prioritize environmental considerations (Milieu) could find themselves being frontrunners in sustainable manufacturing efforts, resonating with environmentally-conscious consumers.
The future of manufacturing, with a keen grasp on 6M components, looks set to accomplish remarkable feats. Governments recognize this potential and frequently establish programs to support industries that are committed to these best practices. The initiatives range from financial grants to expert consultancy, all driving towards a shared goal of raising the bar for the sector. Firms that seize this opportunity to deepen their understanding of the 6M principles will not only thrive commercially but also contribute to a legacy of sustainable, efficient, and high-quality manufacturing for years to come.
Write a comment